The Reason Why DTF Printing is the Future of Custom-made Apparel Manufacturing
Wiki Article
The Increase of DTF Printing: Exploring Its Applications and benefits
The introduction of Straight to Film (DTF) printing modern technology is revolutionizing the custom apparel sector, providing significant benefits and a large selection of applications. As the hunger for custom-made products continues to increase, comprehending how DTF printing can satisfy these developing needs is increasingly crucial.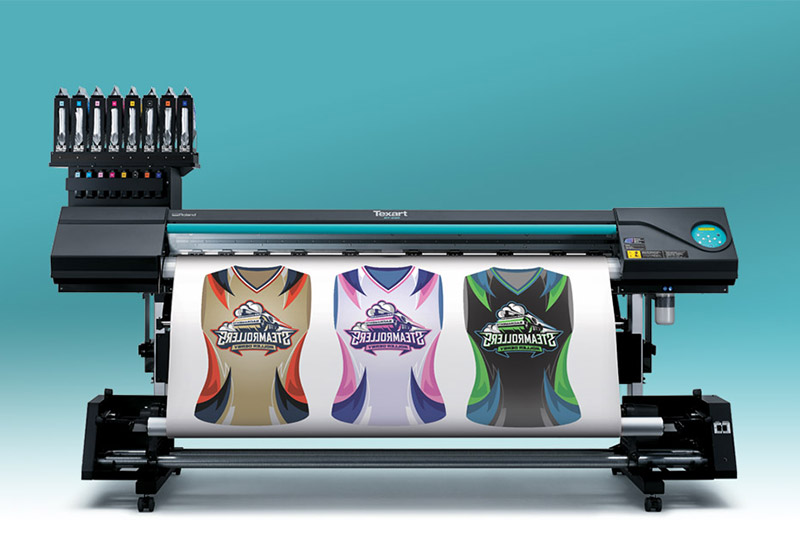
Comprehending DTF Printing Innovation
Comprehending DTF Printing Technology marks a considerable improvement in the fabric printing industry, especially for its convenience and efficiency. Direct-to-Film (DTF) printing is a sophisticated procedure that includes printing layouts onto unique transfer films, which are then moved onto textile utilizing warm and pressure. Unlike standard approaches, DTF printing does not require pre-treatment of the fabric, allowing an extra structured operations.
Once cured, the movie is put onto the fabric, and a warmth press transfers the layout by using consistent warm and stress. This causes vibrant, high-grade prints that stick seamlessly to various textile types, including cotton, polyester, and blends (screen printing). The technology's ability to produce dazzling and detailed layouts with minimal configuration makes it a game-changer in the fabric printing arena
Key Advantages of DTF Printing
One of the key advantages of DTF printing is its extraordinary flexibility, which permits high-grade prints on a vast array of fabric kinds. This capability extends past standard cotton to consist of polyester, nylon, leather, and even mixed fabrics, making it optimal for diverse textile applications. This adaptability reduces the requirement for multiple printing modern technologies, streamlining production processes and minimizing total expenses.
An additional considerable advantage is the premium print high quality that DTF technology provides. By employing lively, sturdy inks and exact application approaches, DTF prints preserve their color fidelity and sharpness also after numerous washes. This leads to a product that not only looks professional yet likewise stands the examination of time, supplying constant value to both end-users and makers.
Moreover, DTF printing offers a streamlined process, which can lead to boosted performance and productivity. Unlike standard techniques such as display printing, DTF does not need complicated setup or considerable drying out times. This convenience of usage makes it an eye-catching choice for services of all sizes, permitting quicker turnaround times and the capability to take care of small to huge production runs with marginal trouble.
Applications in Custom Garments
In the world of personalized clothing, DTF printing sticks out as a game-changing innovation that allows designers and suppliers to produce bespoke clothing with unparalleled detail and quality. Direct-to-film (DTF) printing has actually changed the custom garments industry by using versatility in design, brilliant color reproduction, and sturdiness. This ingenious technique allows for elaborate layouts to be transferred onto a large range of textiles without compromising the integrity of the material.
One substantial application of DTF printing is in developing customized t-shirts, hoodies, and sports apparel. The capability to publish intricate graphics with fine information and gradients makes it ideal for tailored clothing, such as team uniforms and marketing product. DTF printing is especially advantageous for limited-run orders and one-off items, providing a efficient and cost-efficient service compared to conventional display printing methods (sublimation printing).
Furthermore, DTF printing has opened new opportunities for fashion developers to trying out special patterns and textures, allowing the creation of cutting-edge, avant-garde collections. This innovation also supports small organizations and independent artists by decreasing the barriers to entrance in the customized clothing market. Inevitably, DTF printing is improving the landscape of custom clothing, combining artistic expression with technological development.
Flexibility Throughout Different Materials
Building on the developments in personalized garments, DTF printing's convenience throughout various materials better enhances its allure. Unlike conventional printing approaches, DTF (Direct-to-Film) printing can be applied from this source to an extensive range of substrates, including cotton, polyester, blends, leather, and even hard surfaces like timber and glass. This versatility is accomplished with the unique process where designs are printed onto an unique movie and after that transferred onto the product making use of a heat press. This permits dynamic, top quality prints that preserve their stability across various structures and compositions.The capacity to publish on varied materials opens many opportunities for companies throughout different markets. In the marketing products sector, business can customize a wide selection of products, from lug caps and bags to mugs and phone instances, all with the same printing technology. In the garment industry, DTF printing makes it possible for designers to trying out intricate patterns and vibrant shades on unique fabrics, pushing the boundaries of creative thinking.
In addition, DTF printing's compatibility with different products additionally translates to cost-efficiency and lowered waste, as suppliers can use the same equipment for several applications. This versatility not just broadens the range of item offerings yet additionally enhances functional performance.
Future Leads of DTF Printing
As the market advances, the future potential customers of DTF printing are poised to revolutionize various markets with continual development and technological innovations. The surge popular for customized clothing and marketing items is driving the demand for more effective, flexible, and affordable printing approaches. DTF printing, with its capability to produce high-quality, long lasting prints on a wide range of materials, stands at the forefront of this change.
Emerging trends show that DTF printing will significantly incorporate with automation and AI modern technologies, improving manufacturing speed and decreasing labor expenses. Advanced software application remedies will better maximize layout precision, color matching, and print uniformity, dealing with some of the existing constraints. Additionally, environmentally friendly inks and recyclable transfer films are anticipated to obtain grip, straightening with international sustainability objectives.
Industries past fabrics are also exploring the capacity of DTF printing. The technology's adaptability makes it appropriate for applications in home decor, vehicle interiors, and even medical devices. As r & d initiatives remain to broaden, the range of DTF printing will likely broaden, opening new opportunities for creative and commercial applications. In summary, the future of DTF printing is brilliant, encouraging substantial developments and wider industry fostering.
Verdict

Recognizing DTF Printing Technology marks a significant innovation in the fabric printing market, particularly for its versatility and performance. Direct-to-Film (DTF) printing is an advanced process that entails printing designs onto special transfer films, which are after that here transferred onto textile using warm and more tips here stress. DTF printing is especially advantageous for limited-run orders and one-off items, offering a effective and affordable service compared to typical display printing techniques.
Unlike typical printing methods, DTF (Direct-to-Film) printing can be used to an extensive variety of substratums, including cotton, polyester, blends, leather, and also tough surfaces like timber and glass.DTF printing modern technology is transforming the custom-made clothing industry by offering reliable, affordable, and functional options for generating vibrant designs on different materials without pre-treatment.
Report this wiki page